|
|
wendy
plesniak &
|
 |
|
ravikanth
pappu
|
|
|
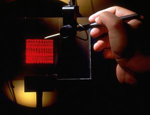 |
|
|
|
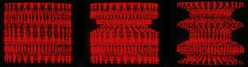 |
|
|
|
|
|
Lathe
has three subsystems: the haptics |
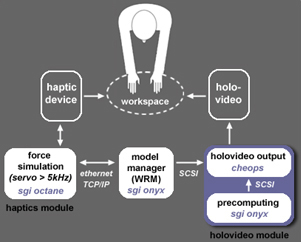 |
|
|
module,
the holovideo module, and the |
|
model
manager. The haptics module runs |
|
our
force simulation and drives the force- |
|
feedback
device. The holovideo module |
|
precomputes
holograms, and drives rapid |
|
local
updates on the holovideo display. |
|
The
model manager keeps the visual and |
|
haptic
representations in sync. |
|
The
force simulation runs at an average |
|
servo
rate of 5kHz, and the holovideo |
|
update
rate is 10fps. The system operates |
|
with
1s of lag between haptic and hologram |
|
updates.
Thus, typically, as a person lathes, |
|
the
surface is immediately felt to change |
|
and
seen to change a second later. |
|
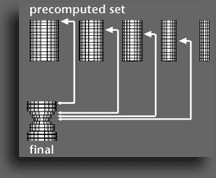 |
|
|
|
Lathe
achieves near-real-time holovideo updates by |
|
using
a set of precomputed holograms of cylindrical |
|
stocks
having different radii. The final image is |
|
then
assembled from appropriate regions of this |
|
precomputed
hologram set, and only changed in |
|
regions
where the model has been affected by a |
|
person's
carving. By making line-level changes, we |
|
avoid
recomputing the entire 36MB holographic |
|
fringe
pattern at each update. |
|
Using
such specific precomputed elements permits |
|
only
a limited set of images to be assembled. Our |
|
third
holo-haptic experiment, Poke, addresses |
|
this
problem by using more generalized precomputed |
|
fringes to assemble a more arbitrary final image. |
|
|
|
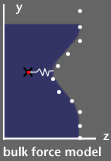 |
|
|
The
force model is given by a 1D |
|
NURB
curve which sweeps out |
|
a
surface of revolution. Pressing |
|
into
the model with the Phantom |
|
stylus
causes a force to be displayed |
|
back to the hand; pressing with |
|
enough
force causes model control |
|
points
to be displaced inward and |
|
the
stock deforms uniformly |
|
around
its circumference. |
|
Finally,
the completed model data
|
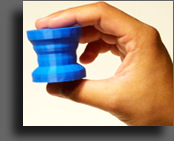 |
|
can
be dispatched to a 3D printer to
|
|
produce
a physical hardcopy of the
|
|
carved
design. The model shown to
|
|
the
right was printed on a Stratasys
|
|
3D
printer. The entire process serves
|
|
as
one example of a future design
|
|
and
prototyping pipeline.
|
|
Selected
references : |
|
|
|
Ravikanth
Pappu and Wendy Plesniak,
"Haptic interaction with holographic video
images", Proceedings |
|
of
the IS&T/SPIE's Symposium on Electronic Imaging, Practical Holography
XII, January 1998. |
|
|
|
Proceedings
of ACM SGICHI Conference on Human Factors in Computing Systems,
April 1998.
|
|
|
|
the
IEEE International Conference on Multimedia Computing and Systems
(ICMCS'99), June 1999.
|
|
Wendy
Plesniak and Ravikanth Pappu, "Tangible,
dynamic holographic images", in Kuo, C.J. (Ed.),
|
|
3-D
Holographic Imaging. Wiley-Interscience (invited, in press).
|
|
Sponsors
of this work include Honda R&D Company, |
|
NEC,
IBM, the Digital Life Consortium at the MIT |
|
Media
Laboratory, the Office of Naval Research |
|
(Grant
N0014-96-11200), Interval Research Corporation, |
|
and
Mitsubishi Electric Research Laboratories. |
|
|
|
 |
 |
 |
 |
 |
 |
 |
 |
 |
 |
 |
|